One of Performance BIM’s very first projects came about after I received a phone call from a colleague I had known for many years. He explained that his company had been asked to model their equipment in Revit and asked if we could help. It did not take long to learn that they had signed a contract many months before requiring them to provide this service, but as with previous projects, they had assumed it could be worked out with the mechanical trade’s BIM team during construction. Unfortunately, not this time…
My colleague is not alone. As the BIM requirements are becoming more stringent, specialty trades are often required to actively participate. Architects and construction managers have embraced a BIM workflow and expect the same from their team members. Owners expect a fully integrated virtual model to be turned over following construction for use in facility management operations. We can no longer ask the construction manager’s engineering group to put a large block in the center of the stage and assume our clash detection participation is complete.
Following the previous post, Demystifying BIM, this article discusses how the BIM process affects specialty contractors in the construction industry and why we should care.
Beyond the Contract
The design and construction contract may be the impetus to integrate a BIM workflow, but the real value is closely tied to the approach. Once we get beyond the frustration of having to learn something completely new or turn our documentation workflow upside down, we can start to see how coordinating our equipment with other trades in a virtual design model can inform discussions and lead to better solutions. How we engage in that process for any given project can be critical to its success.
There are generally two approaches to the coordination process for specialty trades integrating BIM with a current 2D workflow.
- The submittal drawings are developed per a company’s typical workflow, and once complete, the equipment is placed in its “final” location within the virtual design model.
- The equipment is placed in the virtual design model first, then submittal drawings are developed based on those general layouts with the contractor’s typical detailing.
A Tale of Two Projects
Sid's Suspension Services
Sid’s Suspension Services was awarded a project to install a pipe grid, and the construction manager required that they integrate their grid into the virtual design model. Sid has installed hundreds of pipe grids, and the project seemed straightforward. This was the first project that the company was required to actively participate in a BIM process.
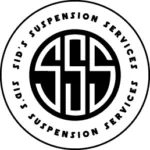
For this project, the modeling occurred after the standard submittal process was complete. While the construction manager worked in a live virtual model, Sid developed his plans and sections in CAD. He then sent the CAD drawings to a third-party modeling company to integrate into the overall building model while the 2d drawings were at the engineering department for final approval. The pipe grid was modeled per the CAD drawings, adjusted, and uploaded into the coordination software. After clashes were identified, the contractor changed the 2d cad drawings; then, the modeling followed suit. The process repeated; however, some issues developed.
- Because the contractor and BIM modeler were using two different “backgrounds,” inconsistencies in the rooms developed, initially placing the CAD pipe grid and modeled pipe grid in slightly different locations. These were identified and corrected, although fixing them slowed down the process.
- The modeling process identified clashes with other trades as intended. However, documenting the corrections required yet another submittal iteration, again slowing the coordination process.
- Equipment modeling fell behind other trades in the building. Because most of those trades’ models were complete, requesting changes when clashes developed was challenging.
Ultimately, clashes were resolved, coordination items were appropriately addressed, and the equipment and services were installed with minimal issues.
Ria's Rigging
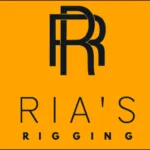
Ria’s Rigging was contracted to replace a motorized rigging system in a historic theatre. The theatre consultant thoughtfully documented the equipment’s layout and desired locations. However, the years of added conduit, sprinklers, and other services required detailed coordination to ensure everything fit.
For this project, the modeling came first. Hoists, blocks, and even cable routing were modeled into the grid area around the existing air ducts and roof drains. The owner, consultant, and contractor met regularly to discuss how to adjust or even change the specific equipment to provide a final product the owner was happy with. The process was iterative and collaborative, and a few lessons were learned.
- While the equipment did not fit as initially anticipated, the exercise forced a conversation of priorities, ultimately resulting in an improved configuration for the owner.
- One component of the design did not fit once the final product was engineered and placed in the proposed location. This slowed the coordination process but ultimately led to a more innovative and streamlined solution.
- All parties were engaged in the process, and visualization helped the owner understand the final product while assisting the contractor to know how they were (or were not) going to access certain areas during installation.
After completing the virtual design model coordination and clash detection process, Ria’s Rigging took CAD exports of the plans and sections from the models. They then developed their engineering details as part of their standard documentation workflow for final submittals. This ensured that the information between the model and documentation was consistent while maintaining Ria’s Rigging’s graphic standards and avoiding duplication of standard equipment detailing. In this instance, the model led the process, and the details followed.
Reactive vs. Proactive
Sid’s Suspension Services took a Reactive approach. The modeling process reacted to an established documentation workflow. Ria’s Rigging, on the other hand, took a Proactive approach. The modeling led the formal documentation. Neither of these approaches is necessarily wrong when factoring in all a specific project’s needs. We at Performance BIM certainly have our bias, and I suspect that BIM experts will quickly point to what I’ve described as “Reactive” is not a proper BIM workflow at all. Both processes ultimately met the project’s needs (and contract requirements). But it is essential to understand the fundamental differences.
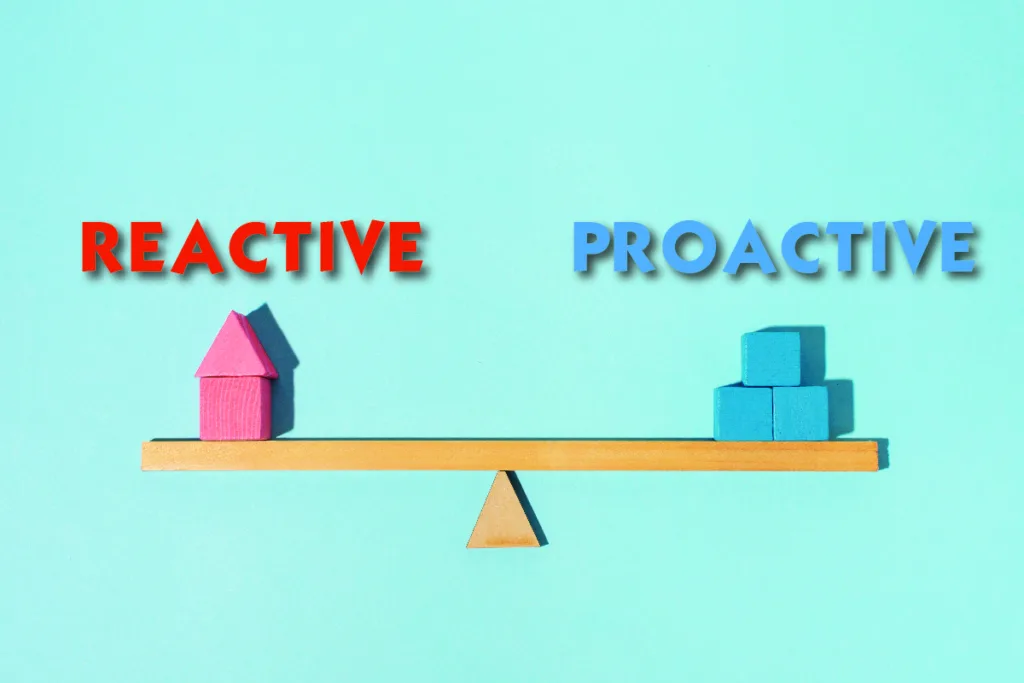
A Reactive approach can be a perfectly acceptable solution for clash detection, especially where the equipment is relatively straightforward, and most conflicts are apparent early on. However, the iterative and collaborative process that is the basis of a BIM workflow is missed, and thus the advantages beyond simple clash detection are gone. Even with the most straightforward project, this lack of collaboration can lead to frustration as one documentation process consistently tries to stay in sync with the other since the information is duplicated in two different mediums.
A commonly overlooked consideration is how this approach could have a potential financial effect. Most contracts that require BIM integration include a provision that requires the trade to place their scope precisely in the location it is placed in the Accepted or Signed Off model following coordination. Any conflicts with other trades are the responsibility of the contractor who deviated from the model. When layouts are created and maintained in two different models or CAD software, the risk of getting out of sync increases substantially. Installers may follow the shop drawings generated in AutoCAD that show equipment in one location while the BIM model has it in another. Contractually, the BIM model wins.
The "Why"
How the BIM process is approached in any given project is as important as engaging in the process itself. Engagement can affect project timelines, engineering time, and the bottom line, whether it is done proactively or reactively. Not every project requires the same approach; some timelines may dictate a hybrid. The goal is to be educated and informed.
And why should we care? It will not be long before most projects require, whether by the architect, general contractor, or owner, a fully coordinated BIM model at project completion (some will argue that we are already here.) Theater equipment must be more than simple cubes that occupy space to allow a facility manager to incorporate dynamic asset tracking (more about this in our next article).
Qualification may very well depend on one’s ability to participate effectively in the BIM process.
This is why we should care.